Memodo @ Meyer Burger: a look behind the sparkling scenes
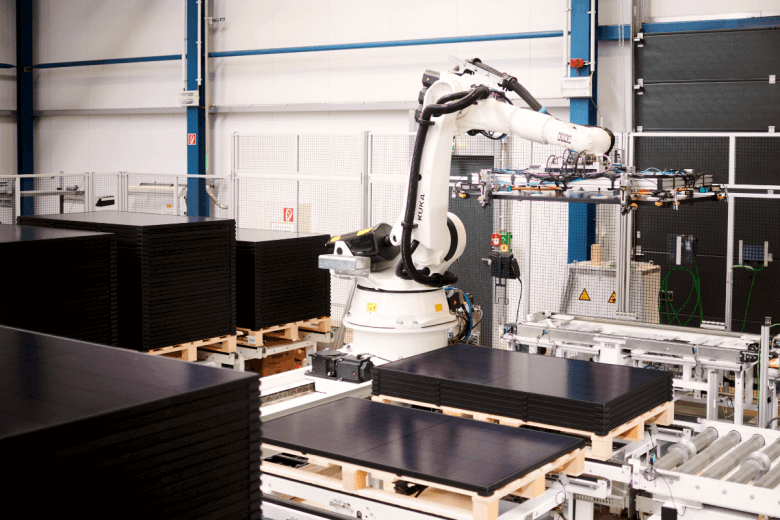
Manufactured in Germany, produced with highly automated in-house systems-technology and sustainable product life cycles - Meyer Burger - is going their own way in many areas. We visited their production facility.
Right outside of Bitterfeld-Wolfen (Saxony-Anhalt) and Freiberg (Saxony), we find two of Meyer Burgers production sites, where the Swiss manufacturer started the renaissance of module production in Germany. Bitterfeld-Wolfen was already home to a large chemical industry during the time of the German Democratic Republic (GDR). This attracted several solar manufacturers in the early 2000s, and the "Solar Valley" was born.
Starting in 2012, a wave of insolvencies swept through Solar Valley, almost bringing it to an end in 2014. But now many solar manufacturers like Meyer Burger are coming back to the region. This is benefiting local skilled workers and experts, who can once again use their knowledge of photovoltaics, from which the companies are now profiting again.
Meyer Burger has also industrialised the production of PERC, TopCon and Heterojunction Technology (HJT) solar cells and made them suitable for mass production. Today, its systems are involved in the production of almost 90 % of PV modules installed worldwide. In 2020, the manufacturer decided to use its systems and technologies exclusively in-house and to produce its own modules without transferring the production know-how to Asia.
From the cell to the module
It all sparkels ─ the production workshop is covered in glass, clean colours and lines. It is located in Bitterfeld-Wolfen, surrounded by other high-tech production facilities. As you step into the workshop, you immediately notice the bright light and vibrant colours. The production facility contains highly automated equipment. Part of the facility is undergoing expansion and construction is underway in the remaining space. The production hall is 40,000 m² in size. This is where Meyer Burger, as the only manufacturer in Germany, produces its own solar cells. In 2022, this amounted to 321 MW. By 2027, production will be expanded to a full 7 GW. Production runs 24/7. Each shift, approximately 40 employees work at this location.
Cell production at Meyer Burger starts with the wafer and the in-house system manufacturing technology. This begins with the optimisation of the wafer surface: saw damage from the wafer cutting process is removed and a desired topological surface (pyramid structure) is created. This ensures better light yield.
In the next step, the cleaned and pre-treated silicon wafers turn into electrically functional solar cells. For HJT solar cells, a layer of amorphous silicon is applied to the front and back of the wafers, as in thin-film solar technology. Thus, the advantages of thin-film technology can be combined with those of crystalline solar cells.
Our group now moves on to the final step of cell production: This is where the conductors are applied to the cells, through which the electrons, i.e., the electric current, will later flow. For this purpose, a silver paste is applied to both sides of the cell. Just like in t-shirt printing, and then dried. Silver consumption at Meyer Burger is significantly minimised by using busbar-less cells.
Change of scene
Leaving the twinkling surroundings and the Solar Valley, we continue our journey to Freiberg. The Meyer Burger module production facility is equally futuristic. Meyer Burger has two production lines in operation here, utilising the full capacity of the hall. A third production line is under construction in a new hall. To produce the modules, the glass is first cleaned and inspected for defects, then the process begins. An embedding material is applied to the glass, which serves as a base for the solar cells.
Before the cells are placed on the module, the "layout" is created. For the layout, the cells are sorted by efficiency level and colour. They are then connected to form strings using Meyer Burger SmartWire technology.
A film with hair-thin wires embedded in it and 10 cells are woven into a string. 6 such strings are placed next to each other on the glass. Thanks to SmartWire technology, there is no need for soldering, which means no thermal or mechanical stress on the cell. Instead, the cells and glass are laminated with the wires and embedding material in a large oven under vacuum at temperatures of around 150°C to form a solid composite. Finally, a welded electrical junction box, including cables and connectors, and a bonded aluminium frame are added before the module undergoes a final quality check.
Meyer Burger operates its own VDE-approved test laboratory so that all certifications can be carried out in-house. For example, the modules are tested for resistance to hailstones up to 35 mm in size or extreme weather fluctuations from -40° to +85° C and permanent hot humidity up to 85°RH over thousands of hours. Even the connectors are not spared.
Our managing director and founder Tobias Wenleder was able to convince himself of the resilience of Meyer Burger modules in the so-called "module breakage test". It took a lot of muscle power and momentum to break the module's glass plate with the 45 kg "wrecking ball" at the third attempt.
Waste, resources & more
Sustainability is an important part of Meyer Burger's corporate culture: all locations are supplied with either green electricity or self-generated energy. New wafer suppliers from Norway operate with electricity from hydropower.
To keep energy consumption in production as low as possible, Meyer Burger has fundamentally rethought many of its production steps. For example, when applying the metal pastes to the solar cells, a temperature of only 200 °C is required, whereas the conventional baking process takes place at up to 1000 °C. Combining the processes of laminating and soldering in the solar module also saves energy during production.
Meyer Burger does not use toxic substances such as lead or other harmful chemicals in its products. This is a plus point when it comes to disposing of the module in the future. In the product life cycle of a Meyer Burger glass-glass module, almost 30 % of the CO2 produced per kWp is saved compared to modules with PERC technology. Packaging waste is reduced by using self-designed, reusable transport boxes for the solar cells.
Partners along the value chain are also consciously selected. Meyer Burger prefers regional suppliers and hopes to be able to source even more components and raw materials from Europe or even Germany in the future. For raw materials that can only be supplied from China, attention is paid to the working conditions there.
Bright prospects for the future
A new production facility is currently being built in the USA and is expected to be operational in 2024. It will supply modules to the American market and is located in the Valley of the Sun in Arizona. It is expected to produce 2 GW of modules per year.
The module market has so far been known for its fierce price wars, with Asian manufacturers leading the way. While there are punitive tariffs on imports of glass, for example, finished modules can be imported easily. But the turning point has come, and the focus is now on technology and quality. Meyer Burger is very well positioned in this respect.
Own experience in machine manufacturing, production technologies and approaches underline their independence. And the wheel of innovation continues to turn: together with the CSEM in Switzerland, the Helmholtz Centre Berlin, the Fraunhofer ISE and the University of Stuttgart, Meyer Burger is working on new technologies such as the back-contact solar cell and the perovskite tandem technology. With this information, we leave the bright shining halls of Meyer Burger.
In summary
- The Memodo team visited Meyer Burger at its production sites in Bitterfeld-Wolfen and Freiberg.
- Cell technologies, cell production, module production, sustainability as well as the production halls themselves were inspected.
- Future plans include the start of module production in the USA and use of new module technologies and playing a major role in module-industry.
Cover Photo: © Meyer Burger